BUSINESS PROCESS RE-ENGINEERING
BUSINESS PROCESS RE-ENGINEERING
-
Business Process Re-engineering
​
Enhance your business process with our experts. We are here to help lean your business processes and bring out the best for your customers and increase the organization's profits.
​
Business Process Re-engineering (BPR) focuses on the analysis and design of workflows and business processes within an organization. It aims to help organizations fundamentally rethink how they do their work in order to improve customer satisfaction, reduce operational costs, and increase your competitive edge. It deals with understanding, identifying, analyzing, and improve the existing business processes within an organization to eliminate waste, and standardized the quality of the goods and services.
​
-
Benefits of BPR
​
-
Remove redundancy/inefficiencies
-
Increase productivity
-
Quick turnaround
-
Standardization of all processes
-
Reduce overhead cost
-
Automation of the new processes
​
​
To help your organization with the above benefits, we review the existing process ("AS-IS"), perform process analysis (cost, quality, etc) and develop "TO-BE" process which will be implemented within the aim of increasing the quality and standard of the products and services while being cost-effective. It helps to identify weaknesses while adding value to the produced products and services.
​
BPR seeks to help companies radically restructure their organizations by focusing on the ground-up design of their business processes. a business process is a set of logically related tasks performed to achieve a defined business outcome. Re-engineering emphasized a holistic focus on business objectives and how processes related to them, encouraging full-scale recreation of processes rather than iterative optimization of sub-processes.
Business process re-engineering is also known as business process redesign, business transformation, or business process change management.
​
The Six Key Steps of Business Process Re-engineering
-
Define Business Processes.
-
Analyze Business Processes.
-
Identify and Analyze Improvement Opportunities.
-
Design Future State Processes.
-
Develop Future State Changes.
-
Implement Future State Changes.
​
Tools
​
-
Six Sigma
-
Lean Management
-
Process Mapping
-
TQM - Total Quality Management
-
Simulation
​
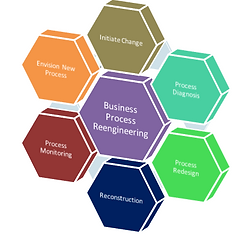
-
Six Sigma
It is a set of management techniques intended to improve business processes by greatly reducing the probability that an error or defect will occur. Six Sigma is a set of techniques and tools for process improvement.
​
5 steps of Six Sigma implementation model
​​
-
D - Define
-
M - Measure
-
A - Analyse
-
I - Improve
-
C - Control
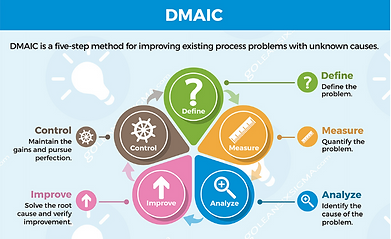
-
Lean Management
A Lean method is a customer-focused approach that promotes the amelioration of organizational operations by eliminating waste. The act of disposing of unnecessary dross in a system maximizes not only customer experience and value but also the organization’s processes.
​
We as well deal with the followings:
​
-
Digital Business Transformation
​
-
Continuous Improvements
​
​
​
​
​
​
We can help your organization to increase efficiency, remove waste/redundancy to increase customer satisfaction and income.
​
​
​
​
​
